Tungaloy Upgrades DrillMeister DMP Drill Heads
Tungaloy claims its 30 new drillheads will improve wear resistance for jobs that require hole diameters ranging from 6.0 to 25.9 mm.
Share




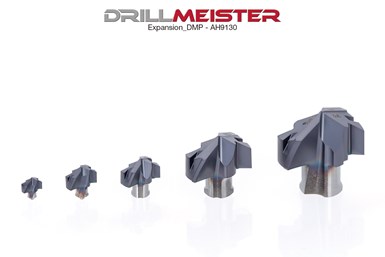
Tungaloy has expanded its DrillMeister exchangeable head drill system by adding 30 more DMP drill heads in AH9130 grade. The company claims this addition will improve the drill’s wear resistance for general purpose applications that require hole diameters ranging from 6.0 to 25.9 mm (.236″-1.020″). This expansion is scheduled to be completed by the end of August 2021.
AH9130 is Tungaloy’s latest physical vapor deposition (PVD) technology specifically designed for high-performance drilling applications. With better wear resistance compared with existing first-choice grade AH725, the grade is said to deliver long tool life in drilling applications, particularly of carbon steel and alloy steel.
Tungaloy claims the DrillMeister exchangeable head drills are a productive, accurate and cost efficient drill series. A single drill body can hold five different styles of drill heads, which are available in general purpose DMP style, DMC for high precision holes, DMH with enhanced drill corner geometry for drilling thin walls, DMF with flat edges ideal for counterboring and DMN for non-ferrous applications.
The DMP style drill head features a 140 degree tip angle with a sharp cutting edge and optimized flute configuration that allows safe chip evacuation and tool stability.
Related Content
-
Custom Workholding Principles to Live By
Workholding solutions can take on infinite forms and all would be correct to some degree. Follow these tips to help optimize custom workholding solutions.
-
Medical Shop Performs Lights-Out Production in Five-Axes
Moving to five-axis machining enabled this shop to dramatically reduce setup time and increase lights-out capacity, but success relied on the right combination of workholding and automation.
-
How to Mitigate Chatter to Boost Machining Rates
There are usually better solutions to chatter than just reducing the feed rate. Through vibration analysis, the chatter problem can be solved, enabling much higher metal removal rates, better quality and longer tool life.