Metal Alloy Analysis Made Affordable
This handheld spectrometer for metal alloy identification features new X-ray technology and a price point that’s attractive to a wider range of manufacturers.
Share





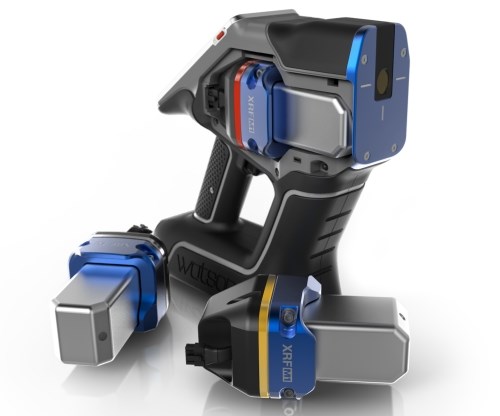
This handheld XRF metal alloy analyzer uses a process similar to static electricity to generate x-rays, bringing the price point down to a level that’s attractive to a wider range of manufacturers.
Traceability is becoming a bigger issue for shops, especially those serving the aerospace and medical industries. Handheld X-ray fluorescence (XRF) spectrometers are commonly used to identify, analyze and tests a broad range of metal alloys for positive materials identification (PMI). Such analysis is commonly performed on raw material as well as finished parts prior to customer delivery to confirm alloy grade. That said, the price point for these devices hasn’t been all that attractive.
says it is the first company to offer an XRF analyzer for less than $10,000. Its Watson XRF device uses a process similar to static electricity (known as the triboelectric effect) to generate X-rays. The company says conventional XRF devices use technology originally developed in the 1800s that relies on bulky, expensive high-voltage transformers to generate X-rays. Tribogenics-effect technology is said to lower both the cost and size for an XRF device using a small (less than 250cc) battery-operated source. Watson also uses replaceable, interchangeable X-ray sources that function much like inkjet cartridges. These cartridges are available in different power levels to address different analyzing needs. They are said to last one to two months and cost $300 to $400.
Related Content
-
Turning Fixed-Body Plug Gages Inside Out
Fixed-body mechanical plug gages provide fast, high-performance measurement for tight-tolerance holes.
-
Orthopedic Event Discusses Manufacturing Strategies
At the seminar, representatives from multiple companies discussed strategies for making orthopedic devices accurately and efficiently.
-
Process Control — Leveraging Machine Shop Connectivity in Real Time
Renishaw Central, the company’s new end-to-end process control software, offers a new methodology for producing families of parts through actionable data.