Got Glue (And UV Light)?
Here’s an effective albeit atypical way to fixture parts such as thin-wall castings that are prone to flexing when conventional mechanical clamps are used.
Share





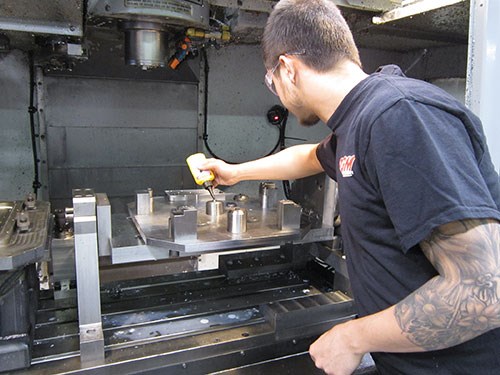
Sometimes shops have to get pretty creative when trying to figure out how best to fixture a part for machining. , in Rochester, New York, leverages an atypical technology to fixture parts such as thin-wall castings that are prone to flexing when conventional mechanical clamps are used.
In short, this technology, available from , uses adhesive to temporarily bond a workpiece to numerous cylindrical grippers installed in a fixture plate. Once the adhesive is cured via ultraviolet (UV) light, the workpiece is securely held at a known datum location in an undistorted, free-state condition. After machining, the adhesive bonds between the grippers and workpiece are easily broken and any excess adhesive is removed from the completed part via a quick, steam-cleaning wash.
Read this story to learn how PGM is using this technology to its advantage.
Related Content
-
How to Mitigate Chatter to Boost Machining Rates
There are usually better solutions to chatter than just reducing the feed rate. Through vibration analysis, the chatter problem can be solved, enabling much higher metal removal rates, better quality and longer tool life.
-
Lean Approach to Automated Machine Tending Delivers Quicker Paths to Success
Almost any shop can automate at least some of its production, even in low-volume, high-mix applications. The key to getting started is finding the simplest solutions that fit your requirements. It helps to work with an automation partner that understands your needs.
-
Shoulder Milling Cuts Racing Part's Cycle Time By Over 50%
Pairing a shoulder mill with a five-axis machine has cut costs and cycle times for one of TTI Machine’s parts, enabling it to support a niche racing community.